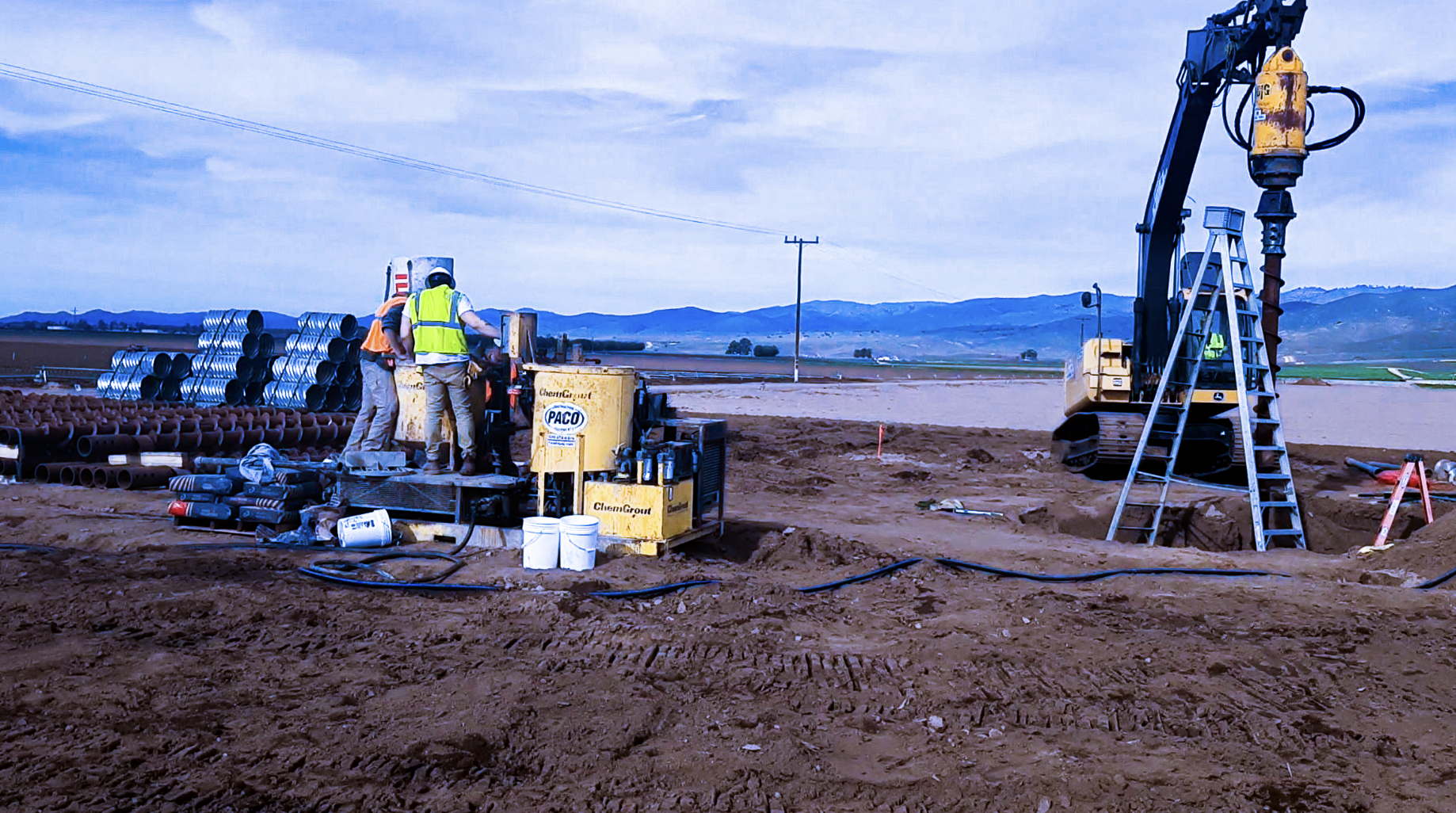
Search for topics or resources
Enter your search below and hit enter or click the search icon.
Our innovative and internationally patented STELCOR Drilled-In Displacement Piles are standing strong under building and infrastructure projects from California to New York, and surpassing traditional piling methods on many fronts.
Taking advantage of the combined super-strength of steel and grout, you can think of STELCOR as an evolved displacement pile that makes installation cleaner and faster.
The top line benefits? You don’t need large or heavy installation equipment. You can install in limited access sites or where vibration can risk structural problems. STELCOR produces no spoils and we’re also finding that, in almost every application, delivers even better results than projected in design.
We picked our top five STELCOR projects from the last few years – you’ll find many more right here: Stelcor Case Study
Built for the First National Bank in 1931, this art deco tower is now not only a designated historic landmark, but the subject of a $275 million investment renovation project to create 193 apartments and a 146-bed hotel. Demolishing a 14-storey annex at the rear to make way for a new ramp to send cars to the parking tower also meant that four new support columns where needed to maintain structural integrity.
As well as this being a historically sensitive site, the installation area was just 11’ wide, ruling out hollow bar micropiles on cost and solid bar micropiles because they would need casing. Both methods would also have created spoils, a risk of flooding and a huge clean-up operation.
“STELCOR DDMs are installed with almost zero vibration. This is why they’re a preferred deep foundation when deep foundations are required near schools, hospitals, historical buildings, or any structure with an already compromised foundation.”
Step in STELCOR: the perfect solution, enabling a cleaner, faster operation and requiring minimal installation equipment.
Find out how easily 24 STELCOR DMMs were installed to a depth of 36 feet…
STELCOR FOR THE FIRST NATIONAL CENTER
Like most businesses, Dole is focused on the future. In this case, by investing $10 million in two wind turbines to produce renewable energy and achieve their goal of net zero carbon emissions by 2030.
The one thing standing in their way? Soil conditions. Wind turbines need foundations that can resist both high tension and compression loads. And achieving the loads on a site that consisted mainly of silty sands with sandy clays was also a challenge. Grouted helicals were considered and ruled out. Mobilizing a dedicated piling rig for two foundations was prohibitively expensive. And the lack of a suitable bearing layer brought other uncertainties.
“The only equipment needed for installing STELCOR DDMs is an excavator or skid-steer, a hydraulic-powered rotary drive head, and a high sheer colloidal grout mixer.”
Working with the specifying engineer, our IDEAL design team configured a STELCOR DDM with a 16″ grout column and a 7″ steel core, and 42 of these were installed using only an excavator with a hydraulic drive motor attachment and a colloidal grout mixer.
You can real the whole story right here:
42 STELCOR® DDMS FOR WIND TURBINES IN CALIFORNIA
Converting an old movie theatre into a climate-controlled storage facility meant adding another five floors, increasing the floor area and reinforcing the existing foundation.
The extra challenge? The piles needed would have to be installed inside the building, close to the existing walls. This all meant other piling methods would either be cost-prohibitive or unable to be installed in low-headroom areas.
“STELCOR really excels in challenging environments where tight access and high-water tables are present.”
Without our STELCOR solution, the building would have had to be demolished and rebuilt. The crew installed 257 STELCOR piles inside the 30-day deadline. And because there’s no vibration, there was no risk to the structure of the 55’ high masonry walls.
Read all about it…
HOW TO SAVE 1.12M DOLLARS AND NOT HAVE TO BULLDOZE A BUILDING IN CHICAGO
Want to know how STELCOR could help your next project?
Send your project info to our IDEAL Design Team. They can put together preliminary design options to give your clients the lowest cost per kip of support: and it costs the client nothing.
Click here to have your project evaluated by a consultant.